The retail and ecommerce sectors are thriving, but with great sales come great returns. In fact, Shopify reports that in 2023 the average return for retail was 14.5%, with online purchases having a higher rate of 17.6% and brick-and-mortar stores having a rate of 10.02%. This reality creates a unique challenge for supply chain professionals: managing reverse logistics efficiently.
The Costs of Returns: An Ever Returning Issue
Returns are no longer just a customer service issue, they’re a supply chain priority. Consider these facts:
- In 2023, U.S. consumers returned approximately $816 billion worth of goods, according to NRF. That’s equivalent to about 23% of total retail sales.
- Processing a return can cost up to 66% of the original item price, factoring in shipping, labor, restocking, and potential discounting for resale.
- Products often lose 10-25% of their value each month they sit in the reverse supply chain. This depreciation affects inventory holding costs, warehousing space, and overall profitability.
For businesses, these numbers represent not just a cost but also an opportunity to innovate and streamline operations.
Reverse Logistics: The Unsung Hero of the Supply Chain
Reverse logistics isn’t just about moving products backward through the supply chain; it’s about creating value. Efficient reverse logistics can:
- Minimize the cost of returns: By reducing touchpoints and leveraging smart systems, businesses can lower overhead expenses tied to reverse processes.
- Reduce environmental impact: Implementing recycling, refurbishing, and resale strategies decreases waste and enhances sustainability goals.
- Enhance customer satisfaction: Fast refunds, hassle-free exchanges, and transparency in return processes boost brand loyalty and trust.
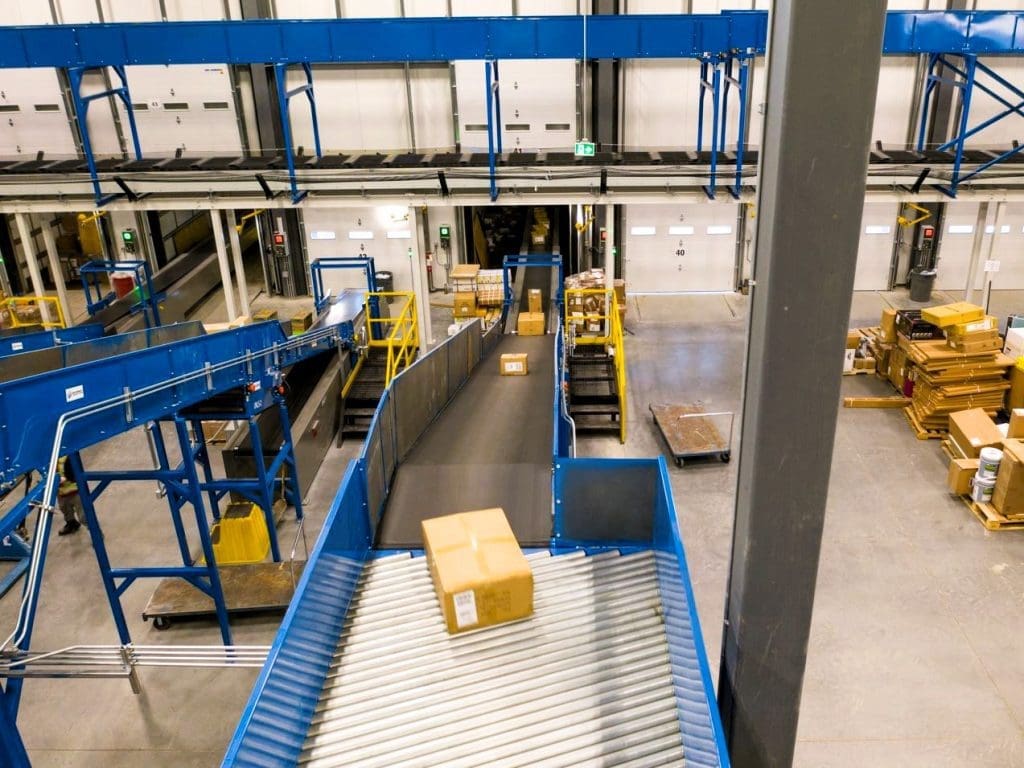
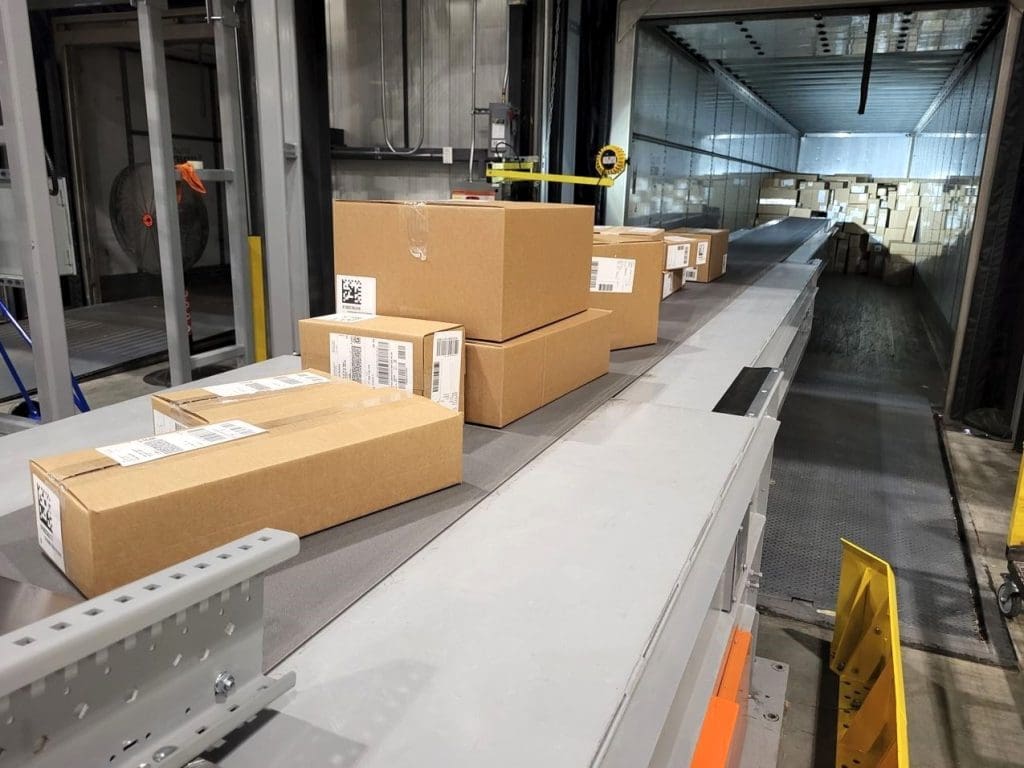
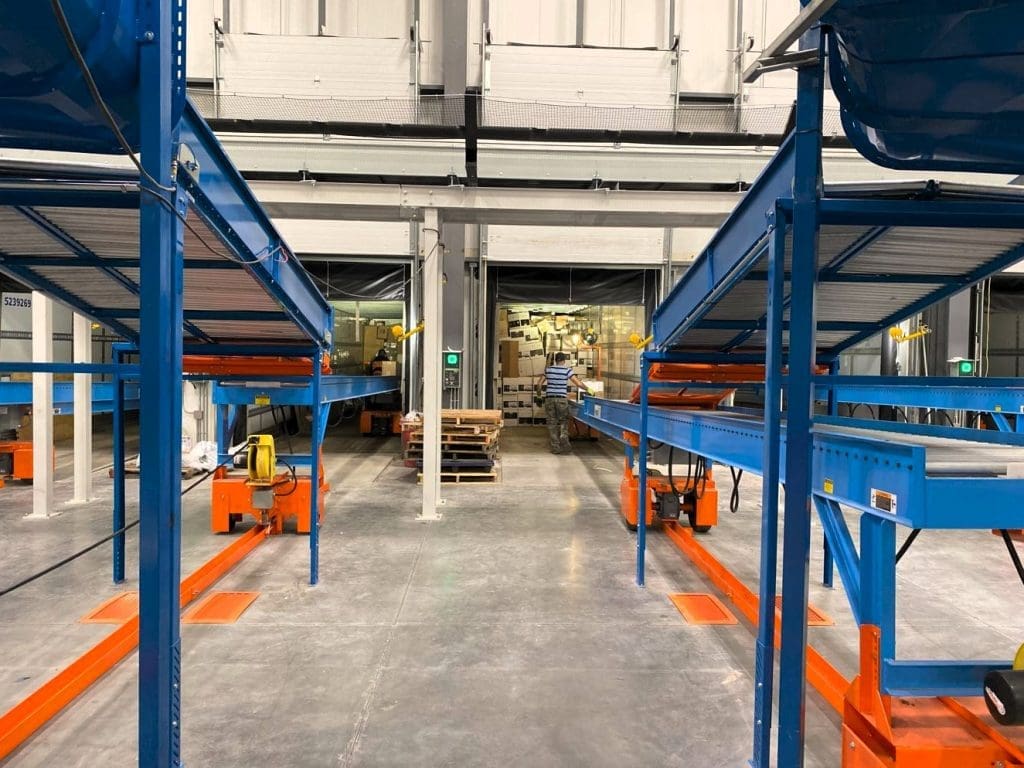
But here’s the catch: reverse logistics is inherently more complex than forward logistics. The unpredictability of return volumes, the variability of item conditions, and the labor-intensive processes of inspection, sorting, and restocking can strain even the most robust operations.
Enter Automation: The Game-Changer
Automation is rewriting the rules of reverse logistics. From advanced conveyor systems to AI-driven software, technology is making returns faster, cheaper, and more accurate. Here’s how:
- Streamlined Processing: Automated systems can quickly sort and route returned items based on criteria such as condition, destination, or resale potential. This speeds up the decision-making process, reducing delays.
- Labor Optimization: Tasks like scanning, labeling, and sorting are traditionally time-intensive. By automating these repetitive actions, businesses reduce manual errors and free up staff to focus on higher-value activities such as customer interactions and strategic planning.
- Data-Driven Decisions: AI and machine learning tools can analyze return patterns, identify trends, and provide actionable insights. For example, identifying common reasons for returns can help businesses improve product descriptions or reduce shipping damages.
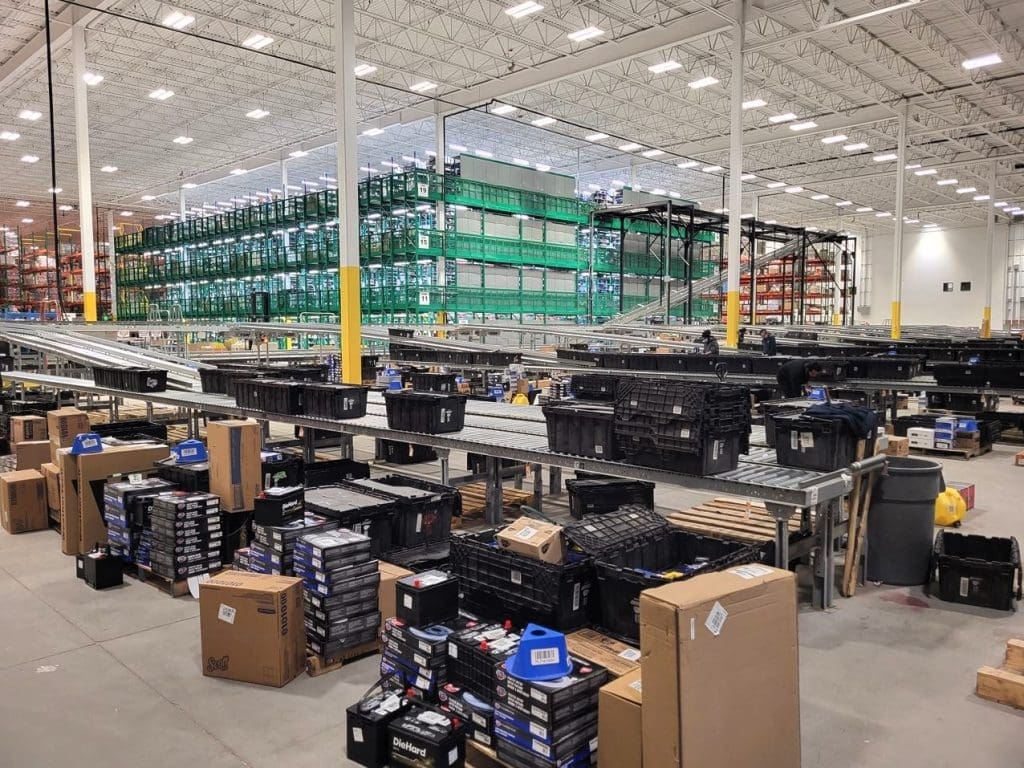
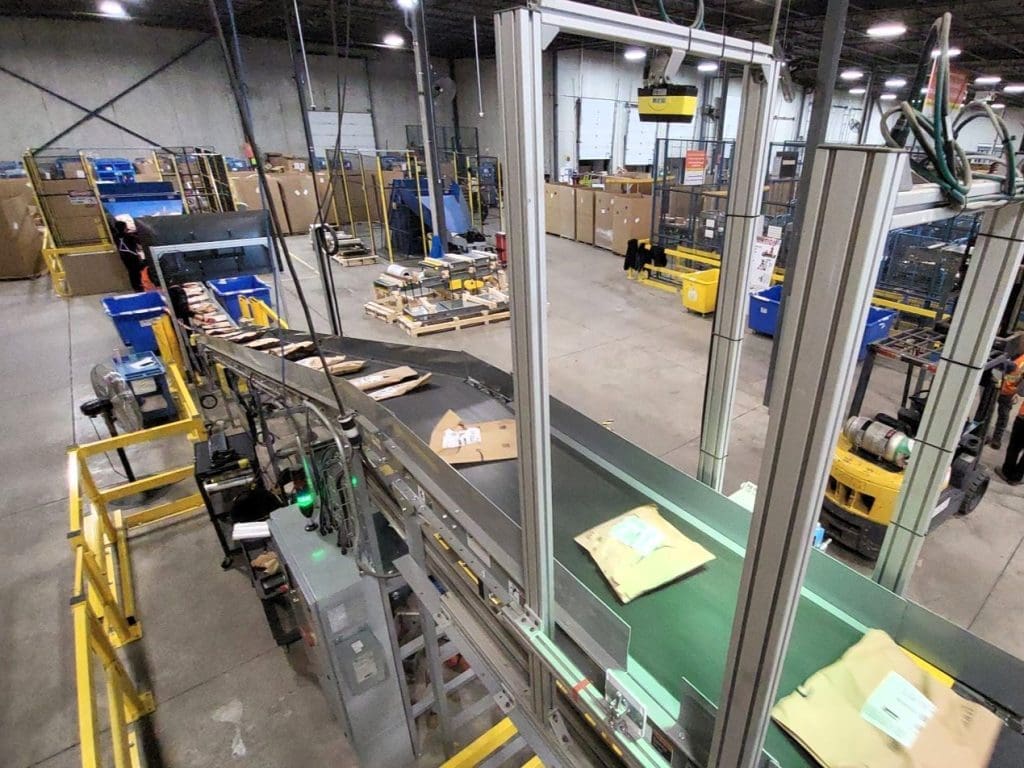
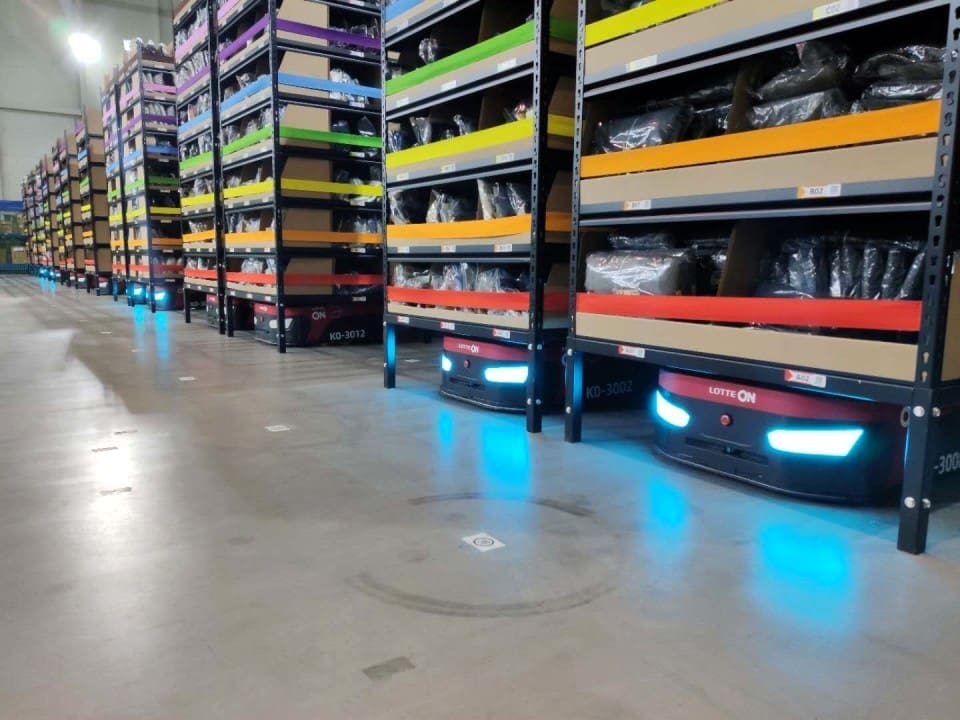
Sustainability Gains: Automation enhances sustainability by efficiently identifying items for resale, recycling, or refurbishment, thereby minimizing waste and reducing the environmental impact of returns.
Success Stories:
Companies embracing automation in reverse logistics are seeing real results. For example:
- A global apparel retailer reduced return processing times by 40% after implementing an automated returns system. This improvement not only cut costs but also enhanced customer satisfaction by speeding up refunds.
- An electronics brand cut labor costs by 30% by deploying AI-powered inspection tools. These systems accurately assessed product conditions, streamlining decisions on restocking versus recycling.
- A leading furniture retailer incorporated automated conveyors and sortation systems, enabling it to handle peak-season returns with 50% greater efficiency compared to manual methods.
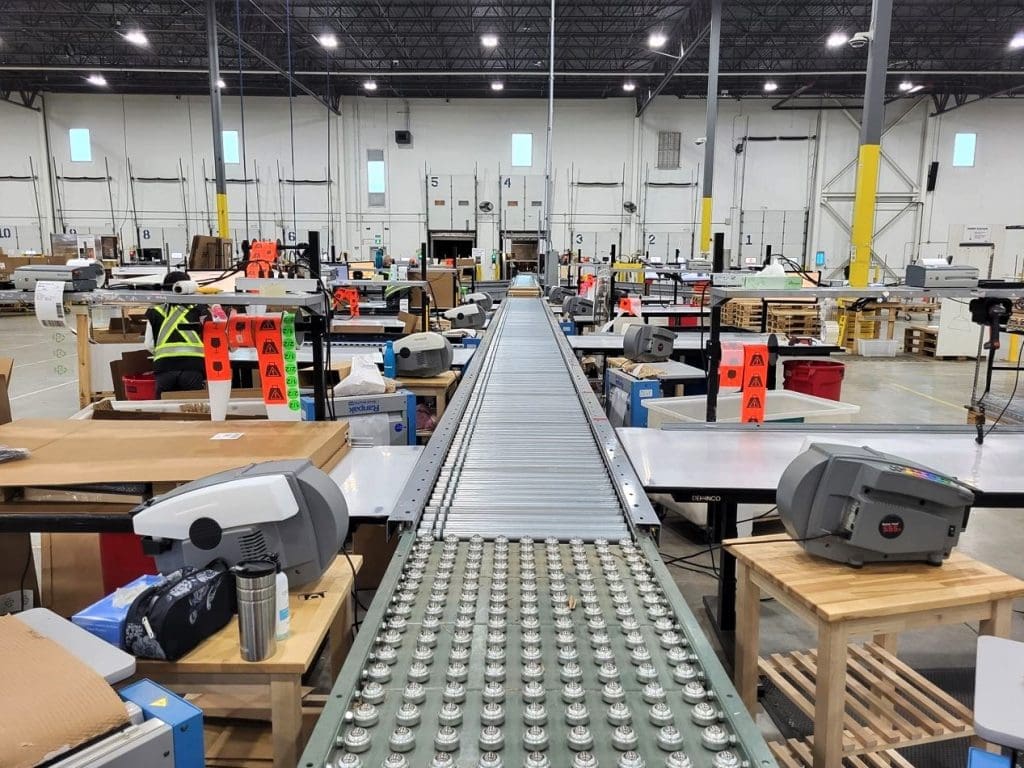
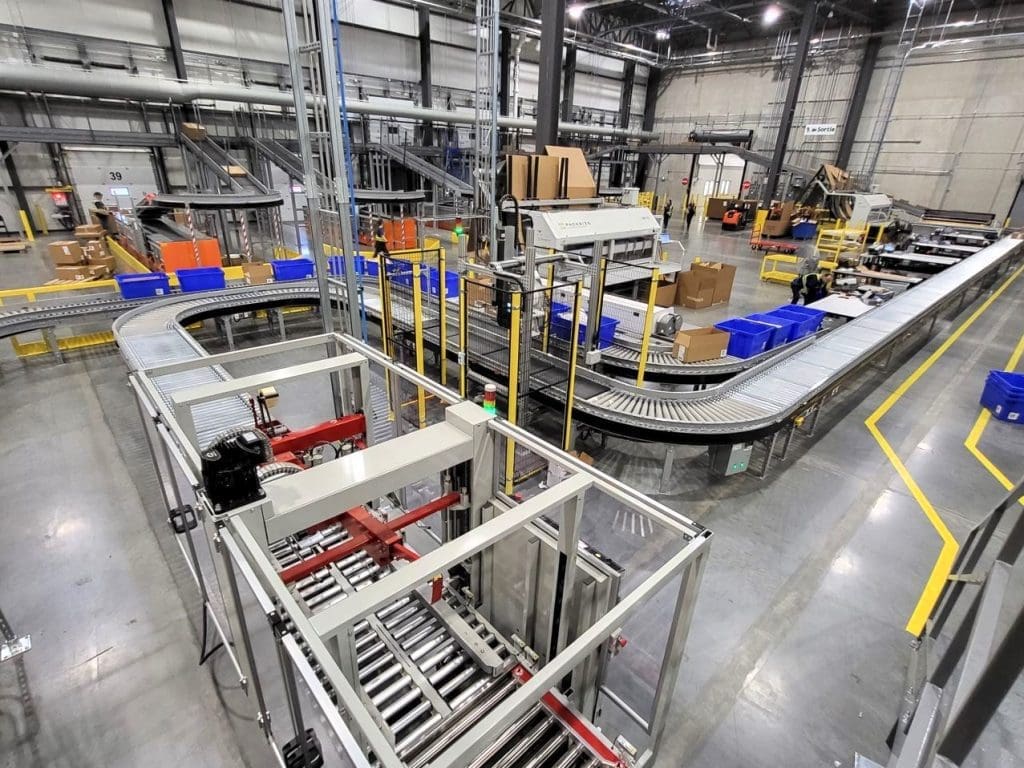

Returns are a fact of life in retail and ecommerce, but they don’t have to be a burden. By investing in automation and optimizing reverse logistics, businesses can transform challenges into competitive advantages. With streamlined processes, reduced costs, and a focus on sustainability, companies can thrive in an ever-evolving market.
How Mainway Can Help:
At Mainway Handling, we specialize in innovative material handling solutions designed to tackle reverse logistics challenges head-on. Our MDR conveyors, robotic sorting systems, and AI integrations are tailored to improve efficiency, accuracy, and scalability. With expertise in optimizing workflows and reducing costs, Mainway is your partner in turning returns into opportunities.
Whether you’re managing high return volumes, striving for greater sustainability, or aiming to reduce processing costs, our team is ready to design a solution that fits your needs.
Let’s Talk: Contact Mainway Handling today to explore how our solutions can make a difference.

Comments are closed