Where Automation Meets Throughput
Our innovative approach to order fulfillment is designed to optimize efficiency, reduce operational costs, and enhance overall warehouse productivity.
What is A Goods-to-Person System
Goods-to-person (G2P) systems are a revolutionary approach to order picking and fulfillment within a warehouse. Unlike traditional methods where workers travel to the items, G2P systems bring the items directly to the operator, significantly reducing walking and searching times.
Applications of G2P
Streamline the picking and packing processes for online orders, meeting the demands of fast-paced e-commerce environments.
Improve efficiency in retail distribution centers by reducing order processing times.
Optimize material handling within your facility, ensuring timely supply of products to your operations.
What We Integrate
Pick Towers, also known as goods-to-person systems or a pick & pass system, is a stand alone structure within a warehouse designed to optimize order picking processes. These systems feature multilevel structures with strategically placed shelves or bins that house products, allowing for efficient storage and retrieval.
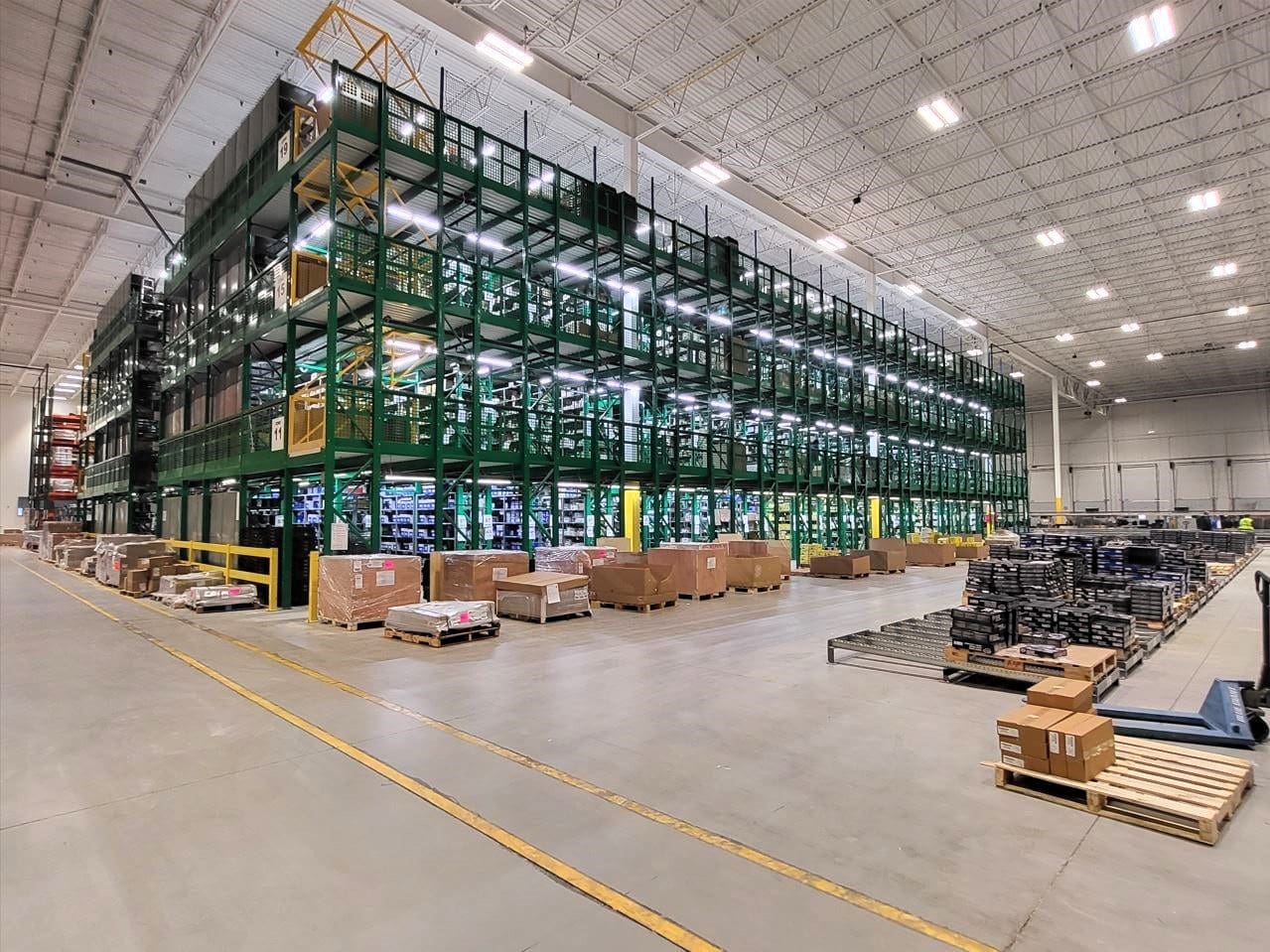
Depending on the specific application, Mainway Handling’s conveyor systems utilize rollers, belts, diverts and pop-ups to transport items. Our range includes powered roller conveyors, belt conveyors, and more, catering to diverse material handling needs. Along with automated sorting and diverting with integrated sensors.
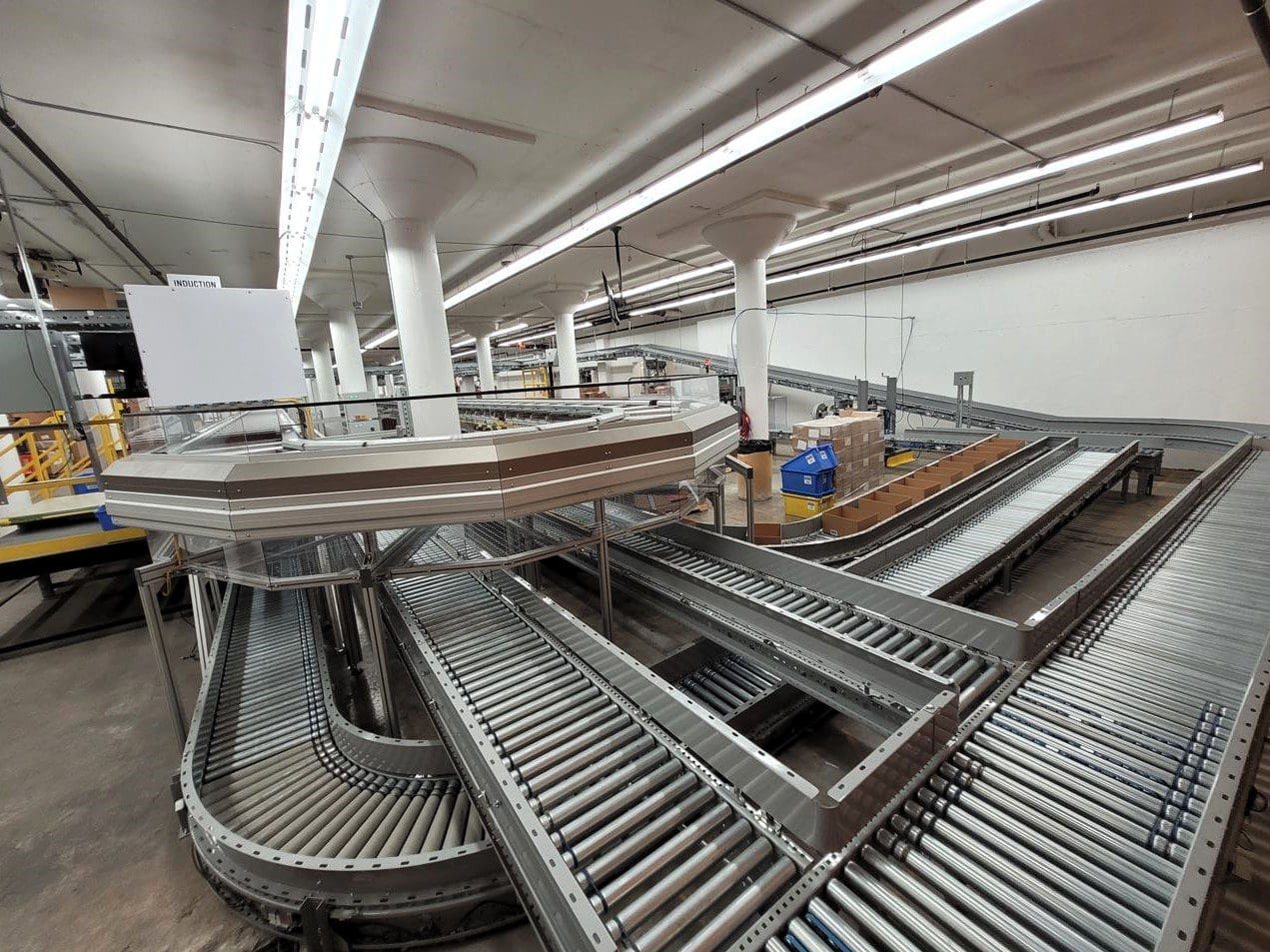
These robust and versatile conveyors are designed to transport items overhead, freeing up valuable floor space and enhancing workflow efficiency. Ideal for manufacturing, distribution, and warehousing applications, with their durable construction, smooth operation, and ability to handle diverse loads, Overhead Conveyors are the perfect choice for improving productivity and streamlining processes in any facility.
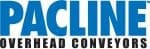
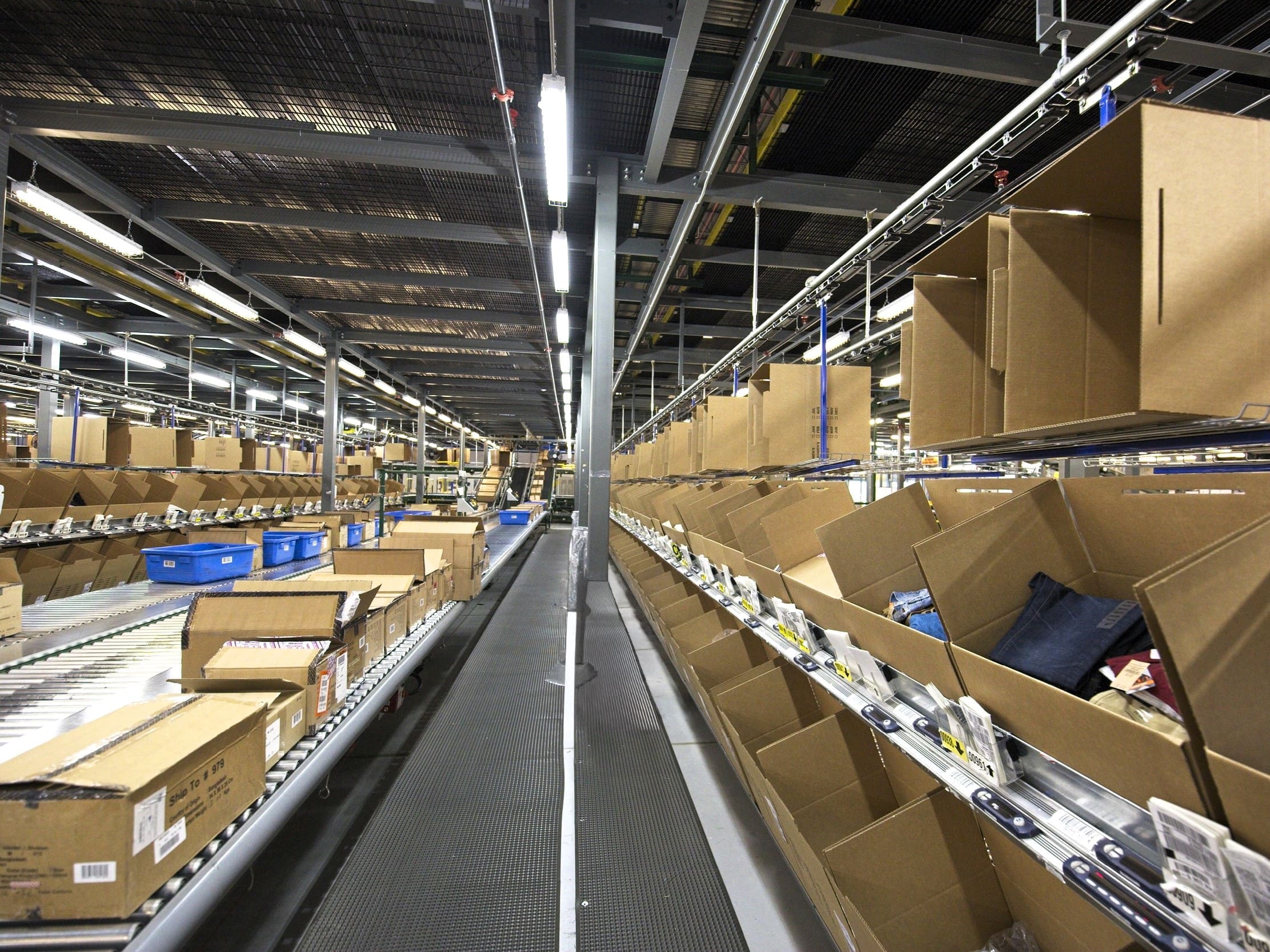
VLMs are vertical towers with trays or carriers that can be automatically retrieved and presented to an operator at an ergonomic workstation. You can improve picking accuracy by securely storing thousands of items in vertical storage, with quick access times, along with reduced walking distances for operators.
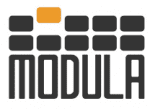
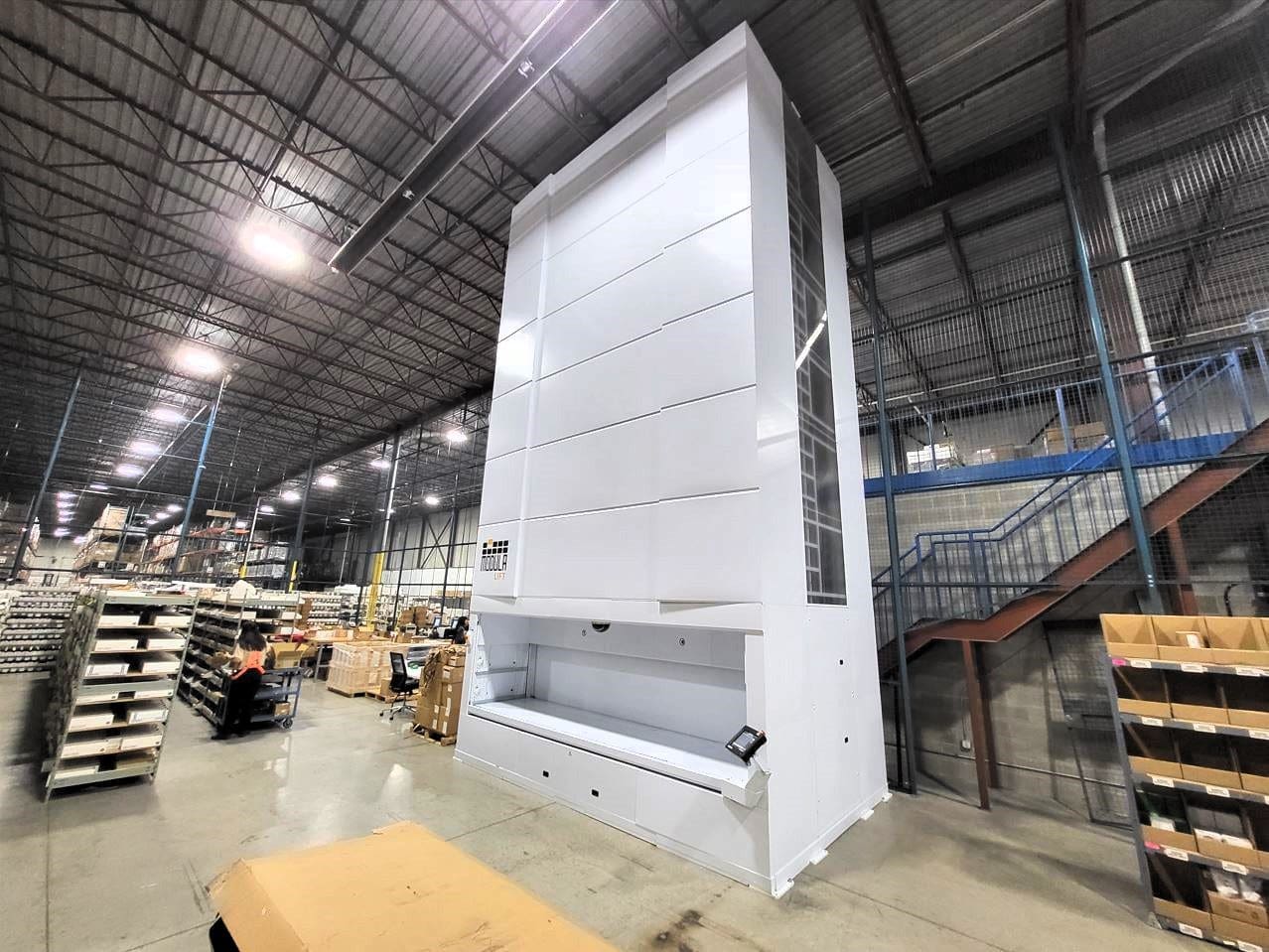
AMRs are mobile robots equipped with sensors and navigation systems that can autonomously navigate through the warehouse to pick up and deliver items. A flexible and scalable solution with the ability to reduce labor costs, adaptability to changing warehouse layouts, and improved efficiency.
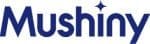
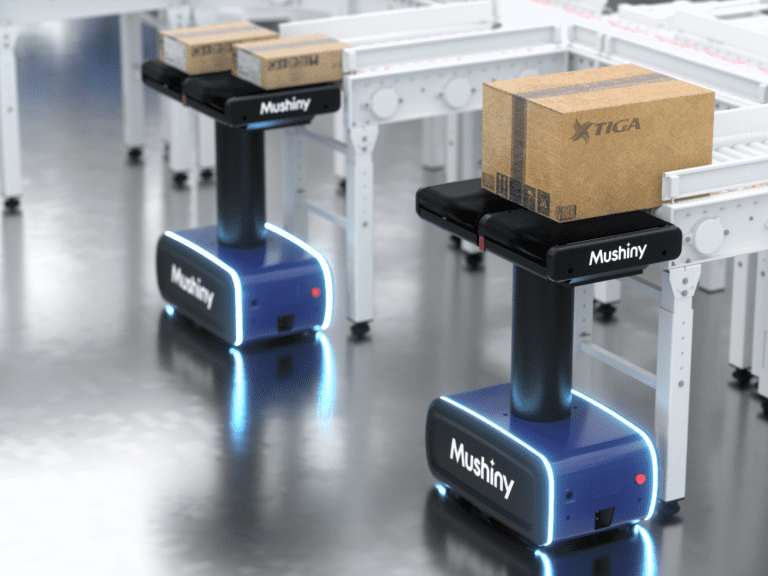
The pinnacle of warehouse efficiency and innovation. Designed to automate the storage and retrieval of goods, AS/RS systems optimize space utilization, enhance inventory accuracy, and significantly increase throughput. By leveraging advanced robotics, precision control systems, and intelligent software, our AS/RS solutions provide seamless integration into your existing operations.
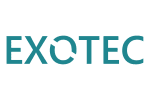
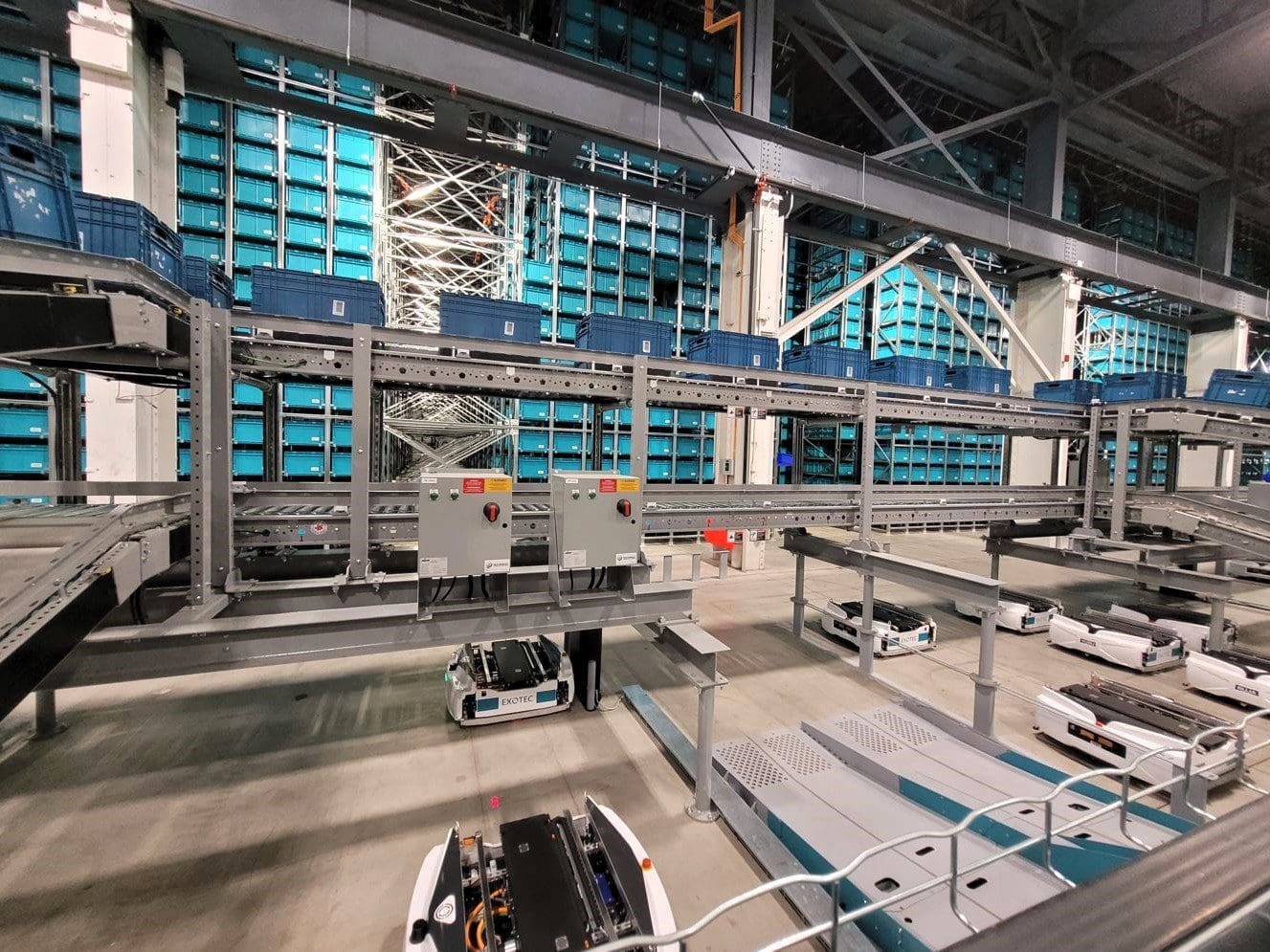
Cutting-edge robotic solution for high-density, high-throughput goods-to-person automated storage and retrieval systems. URBX leverages advanced robotic technology and machine learning software to expedite the order fulfillment process.
The automated nature of our G2P system minimizes the risk of errors and reduces picking times resulting in a significant boost to overall warehouse productivity
How We Integrate
The process begins with the handshake between Mainway’s RTS and the customers ERP. This can include order information, product details, and destination data. Mainway Handling’s systems are equipped to handle a variety of input sources, ensuring flexibility in integration with your systems.
The goal is to reduce retrieval time and increase over all accuracy and efficiency. Products are strategically placed based on factors such as demand patterns, SKU characteristics, and order history.
Mainway Handling’s G2P automation employs various systems to transport goods from storage locations to dedicated pick stations, ensuring a continuous flow of products without the need for manual intervention.
The system presents the order to the operator to significantly reduce the walking time while minimizing the physical strain associated with traditional picking methods. This leads to a more comfortable and productive work environment.
Logistic provenance allows for monitoring the status of items, identifying potential issues, and making data-driven decisions for continuous improvement.
Mainway Handling’s goods-to-person systems are designed for continuous optimization. The system gathers data on order fulfillment performance, allowing for analysis and adjustments to further enhance efficiency over time.
Where they walk less and pick more!